Port Hedland Dredge Optimisation
Channel Risk Optimisation Project
Client: Pilbara Ports Authority
Project Location: Port Hedland, Australia
Completion Date: 2017
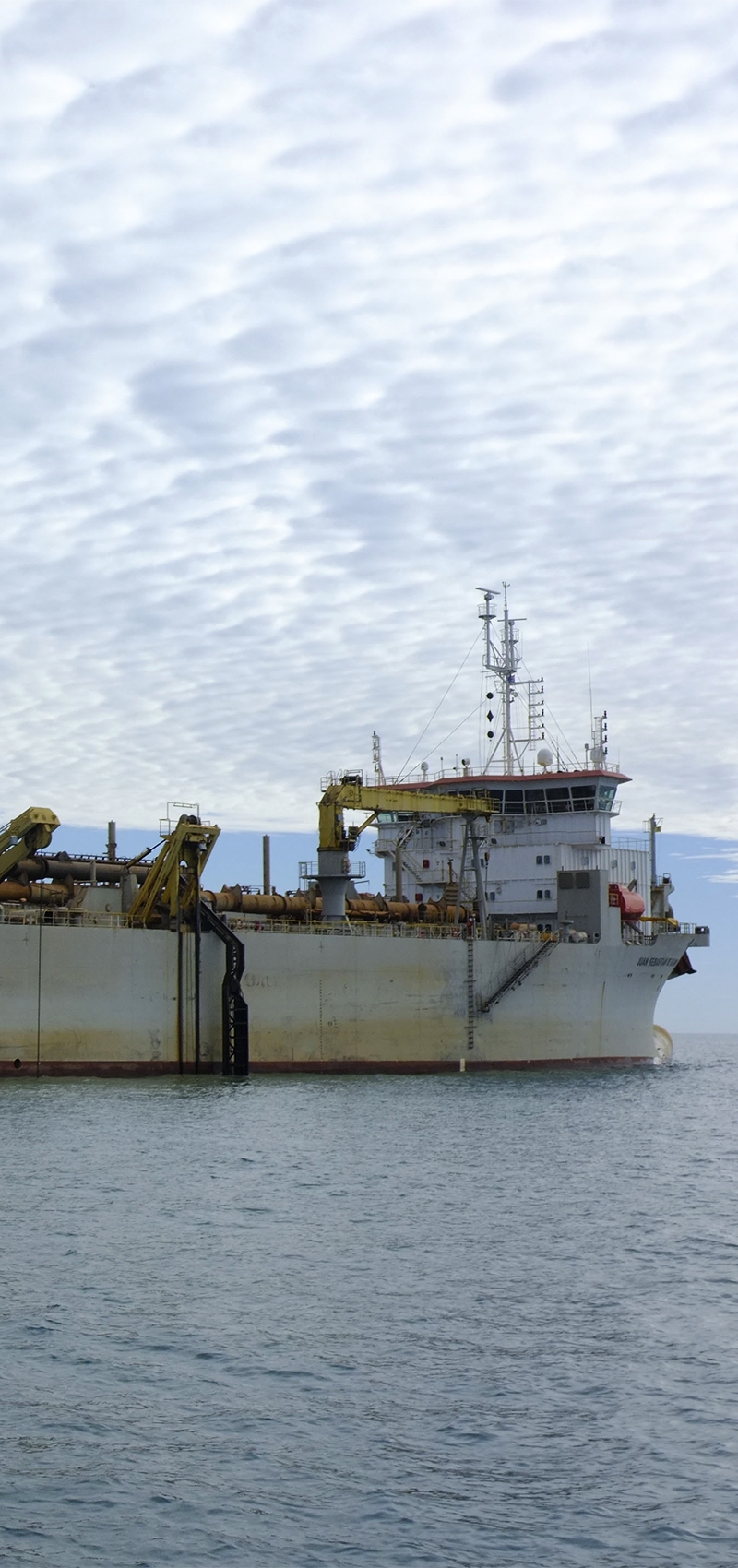
About the Client
The Port of Port Hedland is the world’s largest bulk export port. PPA facilitates approximately $100m of trade through this Port every day, resulting in around 6,000 vessel movements per year. All this is achieved through a uni-directional and tidally constrained 42km channel, with up to eight vessels carrying more than one million tonnes of iron ore and sailing on a single tide.
Overview
OMC undertook a comprehensive dredge optimisation study for a major capital dredging project for the Port of Port Hedland. Utilising DUKC® technology reduced the dredged depth requirements by more than 1m, and the overall dredged area by 90,000m2.
The Business Challenge
The Pilbara Port Authority is progressing the Channel Risk and Optimisation Project (CROP). The culmination of 3 years’ work, CROP is a $120m dredging project with a primary aim of mitigating the risk of disruption to the Port in the event of an adverse incident obstructing the channel.
Iron ore dominates the port’s trade, representing 98% by volume. This is significant not only in the context of the port, but also nationally. The Port of Port Hedland accounts for just under 60% of Australia’s iron ore exports, equating to more than a quarter of the global seaborne iron ore exports.
Any incident within the channel has the potential to block access to the port. Given the value of trade through the port, this would affect not only port operations and its customers, but also state and national economies. Therefore, the risks must be carefully managed having consideration for all the operational factors, including the channel profile, environmental conditions, geographic constraints, and vessel characteristics.
Technical Challenge
- Creating channel depth profiles to optimise the dredging area.
- Individually calculating factors such as wave response, squat, heel etc. as well as considering environmental conditions (waves, tides), vessel dimensions, stability characteristics, speeds and channel configuration.
- Conducting the study based on four draft channel profile options presented by PPA.
The Solution
For the CROP analysis, a baseline scenario was first established by using the existing Port of Port Hedland DUKC® configuration and bathymetry. Vessel transits were simulated over the analysis period for each tide cycle. From each simulation, the available departure drafts were calculated over a tide cycle.
PPA initially presented four draft channel design profile options based on their initial assessment of what would likely be achievable from a capital dredging perspective. OMC performed a preliminary study yielding a preferred profile. From this preferred channel profile, further refinement by the PPA produced an additional four channel profiles for analysis by OMC. Comparing the simulation results with the baseline scenario yielded the expected benefits of each proposed channel profile.
The Outcomes
The DUKC® channel design process enabled the PPA Operations Team to identify a channel depth profile that significantly reduced dredging of geotechnically challenging, and therefore costly, areas by over 90,000m2 without compromising any of the efficiency or safety benefits.
Furthermore, the study highlighted that a DUKC® optimised channel resulted in a considerable benefit over a traditional static UKC approach. For the same level of accessibility, DUKC® reduced the channel depth requirements by an average of 0.63m, and by as much as 1.4m in critical sections of the channel.
Utilising DUKC® technology in the CROP’s design optimisation process, the overall dredging areas, and their associated costs and environmental impact, could be minimised without compromising the benefits.
The Benefits
- Reduced overall dredging area by 90,000m2
- Reduced channel depth requirements by 0.60m-1.40m
- Reduced costs
- Minimised environmental impact